Mechanical stress inside the material is not directly measurable. However, the effects on the respective components are observable. Comparable to a spiral spring affected components change their body geometry. In case of a known spring rigidity or especially in this reference the rigidity of the component, the material stress can be calculated.
Design
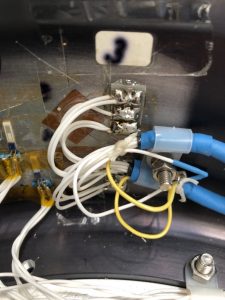
Strain Gauges with PCB
The deformation of the rocket will be detected by strain gauges on the inside of the rocket structure. Due to the spacial orientation of the material stresses and limited effective direction of each strain gauge, an interconnection of a certain number of strain gauges are used. Therefore, they are sensitive to all directions of principal stress (0°, 45°, 90° towards longitudinal axis). Integration of temperature gauges allows the elimination of thermal material expansion in the calculation.
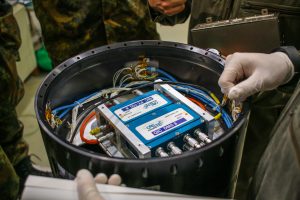
Amplifier
The following amplifiers for the strain and temperature gauges feed the gauges with the requested excitation voltage. Signal filtering and noise reduction can additionally be achieved by a lowpass filter inside the amplifiers. By using a data bus, the transfer of measuring data packages to a FPGA (Field Programmable Gate Array) is ensured.
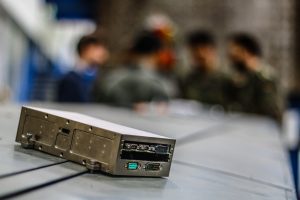
E-Box with MFC-2
The processor, also called Multi-Functional Card (MFC-2) offers the team Software a platform to substantiate personalized visualization and data progressing programs. The focus is on recording and storage of digital data packages. Moreover, the connection between the MFC-2 and the service module enables the steady data transmission between the rocket and ground station for the real-time analysis. The MFC-2 is an exposed circuit board with diverse connections for D-SUB connector. To protect the filigree components an E-BOX made with a certain aluminium alloy. The inside contains three rails for the up to three MFC 2
Tasks
Currently, team Hardware is focusing on the ongoing improvements of the electronical components with the main attention on both electrical and magnetic disturbance. Especially the exposed cables between the strain gauges and the amplifiers are endangered. To that effect a shielding method using ferrite cylinders is currently on testing. Concomitantly with these improvements are frequent tests with the FLOMESS module simulating the harsh environment in the outer layer of the atmosphere. Imitating these, vacuum and thermal chambers as well as a shaker are used. You can easily stay current by liking our Facebook page REXUS-FLOMESS or visit this website.
Member
Achieving a preferably efficient and agile working method to improve the system’s architecture and solve unpredictable incidents, a specialization of each member is existing. As the section responsible Siqiang is the link between the other two technical sections, elaborates new task fields and provides help for the teammates. In the sector practical duties on the experiment module, Armin and Jakob are responsible for the construction of the electrical components and the circuit architecture. Sven deals with the selection of the hardware components including requesting for cooperation with the providers. In the section thermal control due to electrical heat sources Saskia advises the team. Finally, Le Son is responsible for the measurement technology, signal transmission and processing.